Sustain Step of 5S Makes the Process Second Nature
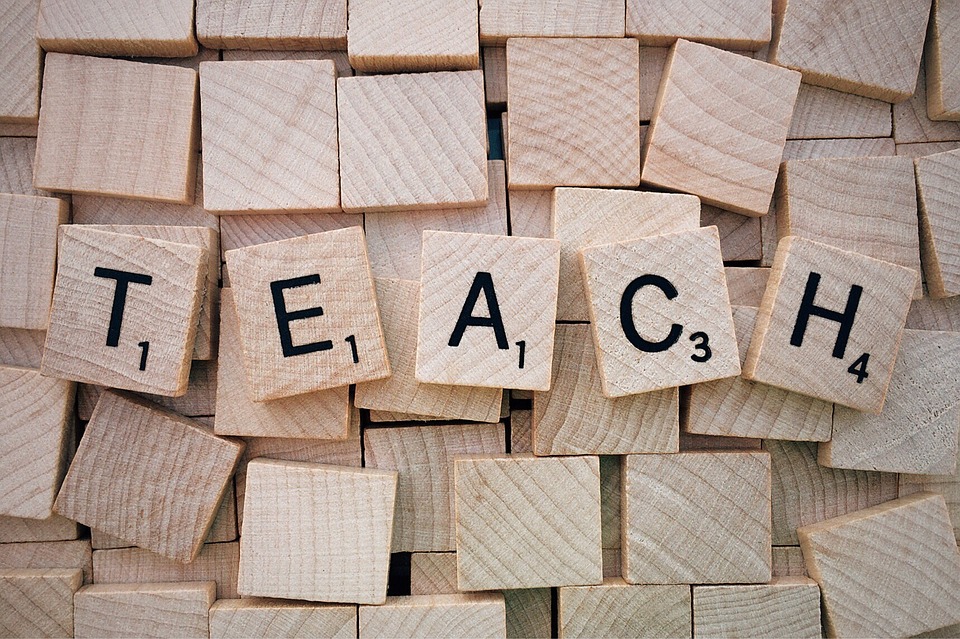
5S helps companies to maximize efficiency within the workplace. Over the past few months, we have been detailing and highlighting the process and we have come to the last step – sustain. The sustain step ensures that the 5S steps taken up to this point are sustained in the long term. Essentially, it is the […]
Standardize Stage Helps Companies Maintain 5S Initiative
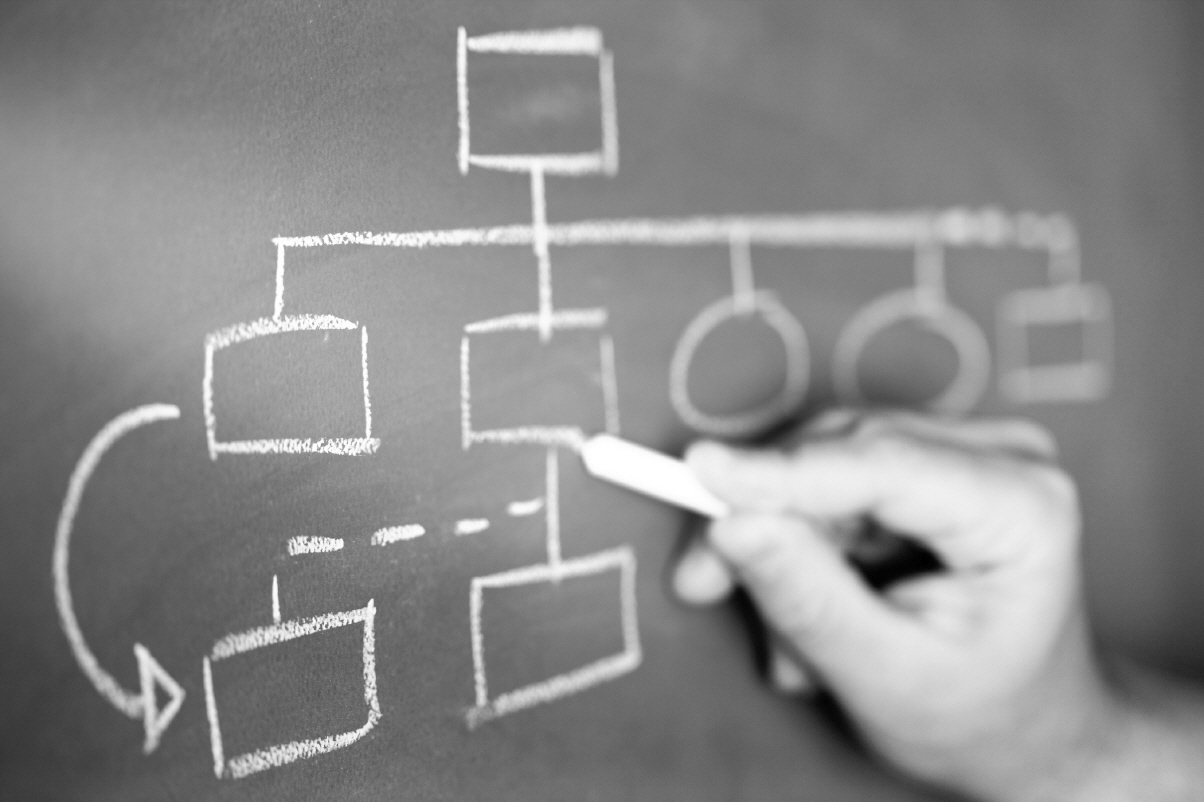
5S Step 4 – Standardize Once you have completed the Sort, Set in Order, and Shine stages of the 5S process, it is time to Standardize. This step will help to maintain the work done in the first three by creating fool-proof processes to keep up with the new work environment. Steps 1-3 implement new […]
Shine Step Allows Companies to Inspect and Improve

Third Step in 5S: Shine Once you have completed the Sort and Set In Order steps of the 5S process, it is time to begin the third step – shine. Cleaning is a very important step in 5S but cannot be completed unless everything is organized and accounted for. Once the plan for each item […]
“Set in Order” Stage of 5S Helps Companies Find Place for All Items in Workplace
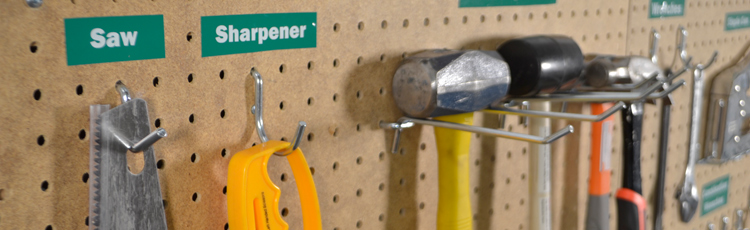
In our latest blog series, we are detailing 5S implementation and what is required of each step. For those who do not know about 5S, it is a program that helps companies reach maximum efficiency. The program stands for sort, set in order, shine, standardize, and sustain. Understanding the concept is the first step towards […]
Step 1: Sort
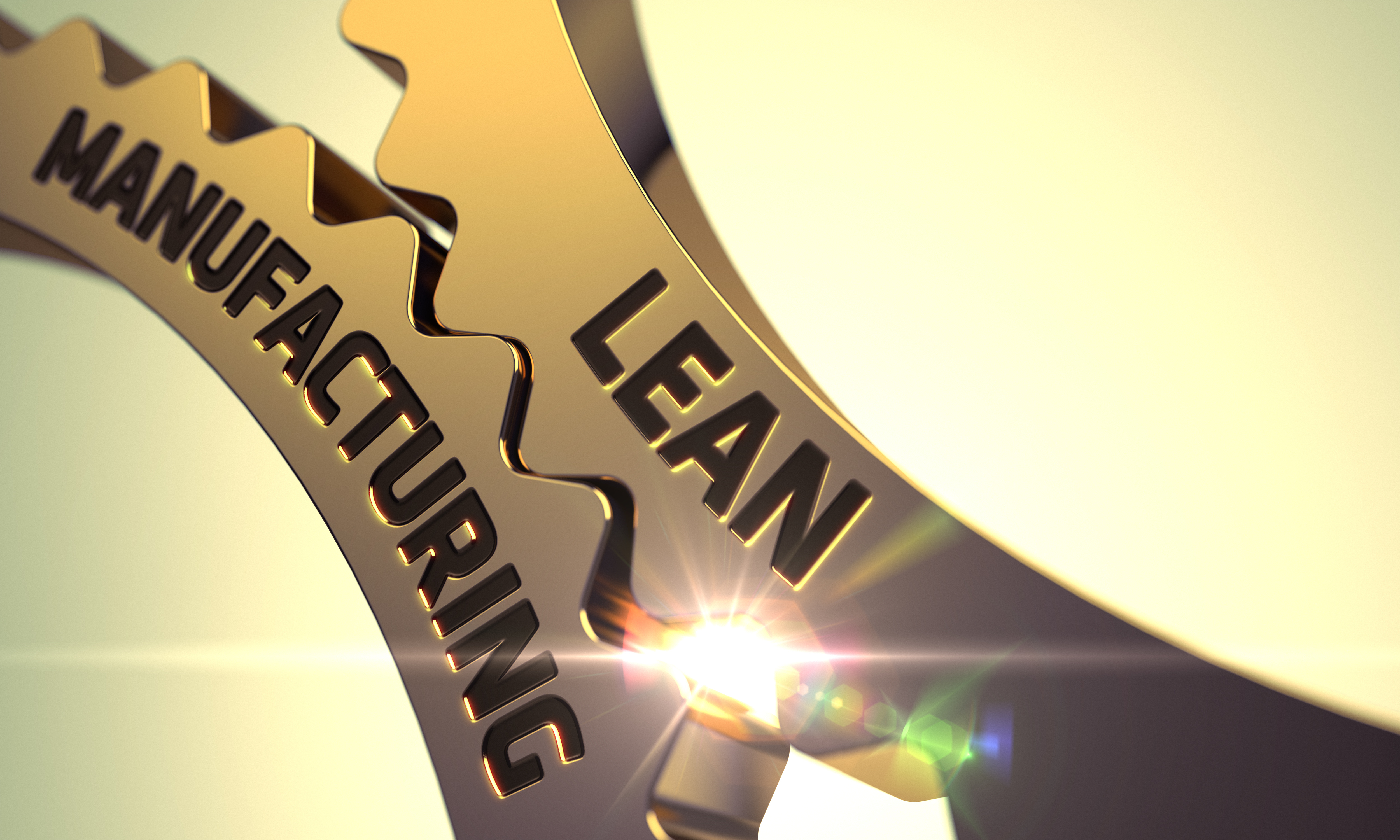
How 5S Helps Companies Reach Maximum Efficiency Starting With the First Step, Sort (seiri) Making smart workplace improvements that 5S requires is not the main reason you do 5S. You make 5S workplace improvements because 5S methods reduce problems and mistakes so every time your work is done, it is your best work. 5S was […]
Bringing Technology to Your Business – Part IV + Bringing It All Together
Over the past four months, we have pondered several ways technology has crucial effects on manufacturing and business operations. Contrary to popular belief, technology transcends computer software; it pervades nearly every aspect of an effectively run business. No matter the size of the company, nor the type of goods or services produced, technology innovation has […]
Lean for Sales (Lean Part 12)
Revenue generation, sales growth, and finding and retaining customers are the lifeblood of all companies. It goes without saying that cash flow improves and customer satisfaction increases when customer jobs, orders, and products are quoted, processed, loaded, and shipped faster and more efficiently. Therefore, let us examine how an important Lean tool, Value Stream Mapping, […]
Lean Part 11: A New Way of Looking at Accounting
Over the past eight months, we have delved into Lean manufacturing principles that focus on eliminating waste and require that all the processes used to manufacture a product occur in sequence. As businesses implement a Lean approach to manufacturing, CPAs have also begun to discover many standard accounting practices no longer hold water. As a […]
Bringing Technology to Your Business – Part IV: Better Business Management
Proven methods to enhance your management reporting systems with custom design and off-the-shelf software Is your documentation scattered? Do you know your key business indictors? What about your yield, cycle times, lead times, and inventory – both product and supply? Do you track your equipment and resource utilization? Are you on top of your serviceability, […]
Lean Part 10: Standardized Work
Standardized work is one of the least popular Lean tools, but also one of the most powerful. It is the collection and implementation of the best practices known to that point, and its application forms the baseline for continuous improvement. As improvements are made, the new standards become the baseline for further improvements, rendering standardized […]