Original publication date: August 13th, 2017 Updated: February 7th, 2024 Material handling encompasses various processes involved in the movement, control, protection, and storage of materials throughout manufacturing. In the realm of lean manufacturing, material handling is recognized as a non-value added activity and a significant source of waste that should be minimized or eliminated. To […]
Material Handling Principles – 10 Steps to Create Effective Working Conditions
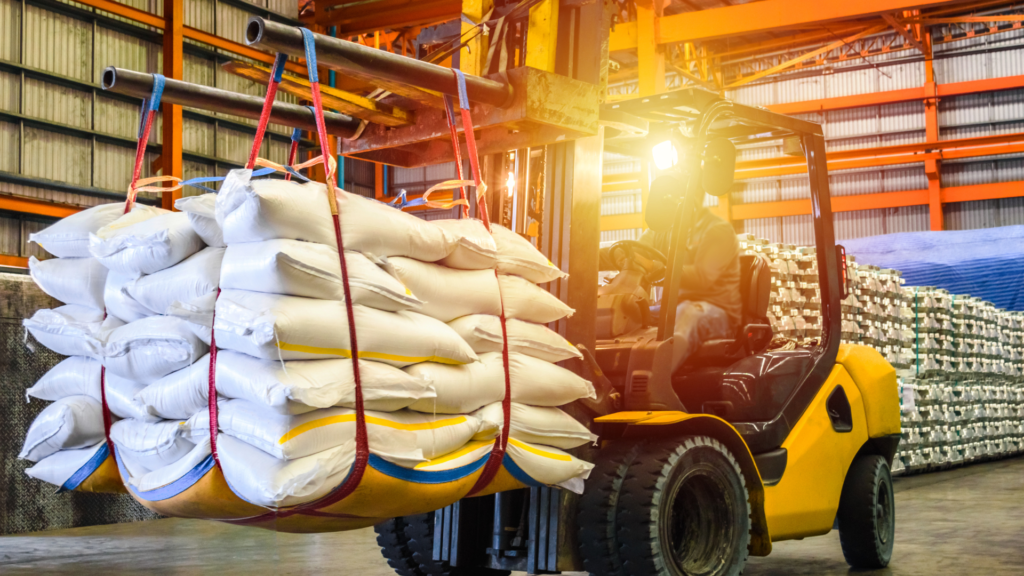